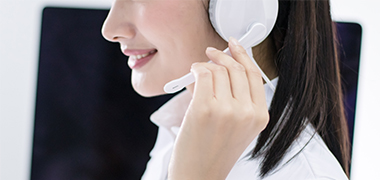
- Contact:Minister Xu
- Mobile:13841408476
- Tel:024-44837288
- Fax:024-44837004
- E-mail:xuming58@126.com
- Web:m.steel-trade.cn
- Address:No.110 XiangHuai Road
Benxi Economic Development Zone
Liaoning Province
Save Your Bearings with Simalube
18 May,2018
Insufficient or over-lubrication can lead to unplanned machine down-time or even
breakdowns. And every maintenance team knows what a breakdown can cause. In fact, it’s
safe to say every associate in any company who is based on production, quality and
consistency knows how deadly breakdown is. It creates a cycle that is hard to thrive in:
Stage 1 – production is driven hard so as to make company successful
Stage 2 – extra attention to production leads to neglect in maintenance
Stage 3 – neglect in maintenance leads to failure of equipment
Stage 4 – production halted and all resources and personnel dedicated to fixing equipment
Stage 5 – loss of money through halted production results in increased production demand
Stage 6 (really Stage 1) – production is driven hard so as to make company successful
It’s a hard loop to get out of! Yet with some simple changes we can do so. Here are the 4
modes of maintenance, and we should all strive to reach the last one:
REACTIVE (BREAKDOWN) MAINTENANCE – that is the case that we describe above. We wait for something to fail, then purchase new or repair. This is the most costly long term of all maintenance modes, and the most infuriating.
PREVENTIVE MAINTENANCE – at timed intervals, specific parts of machines are attended to. This mode helps greatly, but is reliant on doing prescribed actions as opposed to analysis of WHAT is needed. You can equate this to changing your car’s oil at a set mileage rather than if the oil is still good, the filter is still clean, etc. In this mode, you can recognize 50% savings versus REACTIVE.
PREDICTIVE MAINTENANCE – requiring a higher up front cost, the payoff is unmatchable in the long run using Predictive Maintenance. The regular time intervals do more than a prescribed action, but employ many means of analysis (what kind of wear are you seeing, has this happened before, should we change the parameters for this point on the machine, etc.).
PROACTIVE MAINTENANCE – the highest level a company can achieve, here the practices of the maintenance team is put to test, knowing the equipment is secure. Root cause analysis rules, and the control of issues that can stem from root cause are what are systematically controlled. Issues are eliminated before every causing problems (specific training, utilizing supply chain, investment in reliable systems, etc.).
Our automatic simalube lubricators offer you the perfect solution to this problem. The
continuous lubrication ensures low costs, high reliability and many other benefits. The
simatherm induction heaters as well as the simatool toolkits prevent premature bearing
failures that are caused by improper installations.